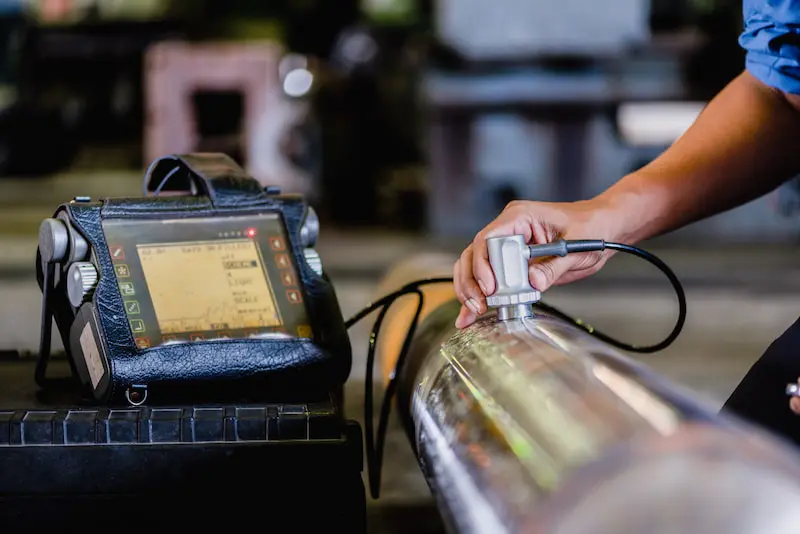
The Future of Inspection: New Technologies in Non-Destructive Testing (NDT)
The industrial world relies heavily on the safety and integrity of its infrastructure. Non-destructive testing (NDT) is critical in ensuring this by enabling inspectors to assess the condition of materials and equipment without causing damage. But the world of NDT is constantly evolving, with new technologies emerging to push the boundaries of what's possible.
This article explores some of the most exciting advancements in NDT, highlighting how they are shaping the future of inspections:
1. Artificial Intelligence (AI) and Machine Learning (ML):
-
Revolutionizing Data Analysis: NDT inspections generate vast amounts of data. AI algorithms can analyze this data quickly and accurately, identifying patterns and anomalies that might escape human inspectors. This can lead to faster and more precise defect detection.
- Predictive Maintenance: AI can learn from historical inspection data to predict equipment failures before they occur. This allows for proactive maintenance, minimizing downtime and saving costs.
2. Robotics and Automation:
-
Enhanced Safety and Accessibility: Robots can be deployed in hazardous environments or hard-to-reach areas, reducing the risk of human exposure to dangerous conditions. This is particularly beneficial in industries like oil and gas or nuclear power.
- Increased Efficiency and Repeatability: Robotic systems can perform inspections with greater consistency and precision than manual methods. This ensures data quality and reduces the possibility of human error.
3. Advanced Sensor Technologies:
-
Improved Data Acquisition: New sensor technologies offer higher resolution and faster data acquisition capabilities. This allows for more detailed inspections and the detection of even smaller defects.
- Emerging Sensors: Techniques like terahertz imaging and ultrasonic guided waves are being explored for their potential in NDT applications. These offer unique capabilities for inspecting certain materials or complex geometries.
4. Integration and Interconnectivity:
- The Power of Big Data: The future of NDT lies in integrating data from various sources, including NDT inspections, sensor readings, and maintenance records. This big data approach can provide a holistic view of an asset's health, enabling better decision-making for repairs and maintenance.
- The Rise of the "Internet of Things" (IoT): NDT equipment is becoming increasingly interconnected, allowing for real-time data transmission and remote monitoring. This facilitates faster response times to potential issues and improves overall inspection efficiency.
Benefits of New NDT Technologies:
- Improved Accuracy and Reliability: New technologies lead to more precise and dependable inspections, minimizing the risk of missed defects.
- Enhanced Safety: Automation and robotics can protect inspectors from hazardous environments.
- Increased Efficiency and Cost-Effectiveness: Faster inspections and predictive maintenance can save time and money.
- Better Decision-Making: Advanced data analysis provides valuable insights for optimizing maintenance strategies.
The Future is Bright
The future of NDT is brimming with exciting possibilities. By embracing new technologies, the industry can achieve a new level of accuracy, efficiency, and safety in ensuring the integrity of critical infrastructure. As these technologies continue to develop and integrate, we can expect even more groundbreaking advancements that will reshape the future of inspections.