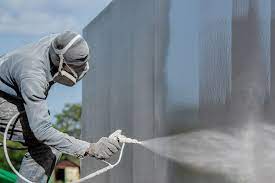
Corrosion Resistant: Ultimate Guide to Protective Coatings in Kuwait
The economic and safety costs associated with corrosion are staggering, highlighting the critical role protective coatings play in safeguarding Kuwait's valuable assets.
The High Price of Corrosion in Kuwait
Corrosion's impact in Kuwait is far-reaching. It weakens bridges and buildings, necessitating costly repairs and maintenance. In the oil & gas sector, pipelines and storage tanks become susceptible to leaks, leading to production losses and potential environmental damage. Perhaps most alarming is the risk of structural failures due to corrosion, jeopardizing public safety.
The exact cost of corrosion in Kuwait is difficult to quantify, but studies worldwide suggest it can devour a significant portion of a nation's GDP. Kuwait can significantly reduce these financial burdens by investing in effective corrosion control measures, like protective coatings.
Understanding the Kuwaiti Environment: A Corrosion Catalyst
Kuwait's unique environment is a breeding ground for corrosion. The high temperatures that dominate most of the year accelerate the rate at which metals degrade. Additionally, the intense sunlight emits ultraviolet radiation, which can further weaken certain coatings. The ever-present salt spray along the coast and the abrasive particles carried by sandstorms inflict further damage on exposed metals.
These environmental factors, working together, create a perfect storm for corrosion, making protective coatings an essential line of defense for Kuwait's infrastructure and industrial assets.
Protective Coatings: Fight Against Corrosion
Protective coatings act as a valiant shield, safeguarding metals from the relentless assault of corrosion. But how exactly do they achieve this remarkable feat?
These coatings create a physical barrier between the metal substrate and the corrosive elements in the environment. They act like a suit of armor, preventing moisture, salt, and other contaminants from reaching the metal's surface. There are two main categories of protective coatings: barrier coatings and sacrificial coatings.
Barrier coatings, as the name suggests, form an impenetrable layer that isolates the metal from the environment. Common examples in Kuwait include high-build epoxy coatings and polyurethane coatings. These robust coatings boast excellent adhesion and are formulated to withstand the harsh Kuwaiti climate.
Sacrificial coatings, on the other hand, take a more selfless approach. They are made from a metal that corrodes more readily than the substrate they are protecting. As the sacrificial coating deteriorates, it shields the underlying metal, essentially sacrificing itself for the greater good. Galvanizing, a popular method in Kuwait, employs zinc as the sacrificial metal to protect steel.
Choosing the right protective coating for a specific application in Kuwait requires careful consideration. In the next section, we'll explore the key factors that influence this decision.
Selecting the Right Protective Coating for the Kuwaiti Arena
Choosing the most effective protective coating for a Kuwaiti project requires a strategic approach. Several factors come into play to ensure the chosen coating provides optimal defense against the relentless Kuwaiti environment.
-
Substrate Selection: The type of metal being protected plays a crucial role. For instance, high-build epoxy coatings excel on steel structures like bridges, while fusion-bonded epoxy coatings are ideal for underground pipelines due to their superior resistance to moisture ingress.
-
Exposure Environment: Understanding the specific environment the coated structure will face is paramount. Onshore applications exposed to constant sunlight and salt spray require UV-resistant and waterproof coatings. On the other hand, offshore structures necessitate coatings that can withstand the harsh marine environment.
-
Coating Lifespan and Performance Requirements: Different coatings offer varying lifespans. High-performance polyurethane coatings can provide extended protection for decades, while some simpler options might require more frequent reapplication. The desired lifespan should be weighed against the project budget and maintenance feasibility.
-
Regulations and Standards: Kuwait adheres to strict regulations set by organizations like the Kuwait Oil Company (KOC) and the Kuwait National Petroleum Company (KNPC). These regulations often specify approved coating types and application procedures for projects within their purview. Consulting these standards is crucial to ensure compliance.
Popular Protective Coatings in Kuwait
The Kuwaiti construction and oil & gas industries rely on a well-armed arsenal of protective coatings to combat corrosion. Here are some of the most frequently deployed soldiers in this fight:
-
Epoxy Coatings: These versatile warriors come in various formulations, offering a high degree of customization. High-build epoxy coatings are renowned for their exceptional adhesion and ability to withstand harsh environments. Fusion-bonded epoxy (FBE) coatings, designed explicitly for buried applications, provide excellent protection against moisture and chemical attack, making them ideal for underground pipelines.
-
Polyurethane Coatings: These robust defenders offer outstanding resistance to UV radiation, making them well-suited for Kuwait's sun-drenched landscapes. Additionally, high-build polyurethane coatings boast impressive chemical resistance and mechanical strength, making them a popular choice for structures exposed to industrial environments and harsh chemicals.
-
Galvanizing: This time-tested technique employs zinc, a more reactive metal, as a sacrificial shield for steel. The zinc layer corrodes first, protecting the underlying steel for extended periods. Hot-dip galvanizing, where steel is dipped in molten zinc, is common. Thermal spraying, another form of galvanizing, utilizes a high-velocity spray to apply a zinc coating, offering greater flexibility for on-site applications.
-
Other Protective Measures: While epoxy, polyurethane, and galvanizing are prominent players, the fight against corrosion doesn't stop there. Cladding, where a corrosion-resistant metal sheet is bonded to the substrate, offers exceptional protection for critical infrastructure. Heat shrink sleeves, pre-shrunk plastic tubes that conform to the shape of a pipe upon heating, provide a cost-effective solution for pipeline corrosion control.
Application and Maintenance of Protective Coatings
The efficacy of protective coatings hinges not only on the chosen weapon but also on the skill of its application and the vigilance of its maintenance. Here's a breakdown of these crucial aspects:
Surface Preparation: The Foundation for Success
The metal surface requires meticulous preparation before any protective coating can be applied. This is akin to prepping a canvas for a masterpiece. Techniques like sandblasting or grit blasting remove dirt, rust, and mill scale, creating a clean, roughened surface that optimizes adhesion. Degreasing ensures the absence of oils and contaminants that could compromise the coating and metal bond.
Application Techniques: Wielding the Weapon with Precision
The application of the chosen protective coating requires expertise and adherence to proper techniques. Spraying, brushing, or dipping are the most common methods, each with its advantages and ideal situations. Trained professionals with the necessary equipment and experience ensure a uniform, high-quality coating that maximizes its effectiveness.
Maintenance: Eternal Vigilance is the Price of Protection
Just like any line of defense, protective coatings require regular inspection and maintenance to maintain their integrity. Visual inspections can detect cracks, blisters, or other signs of deterioration. Instruments like ultrasonic thickness gauges can measure the remaining coating thickness, allowing for timely reapplication before the metal becomes vulnerable. Following a well-defined maintenance plan ensures the protective coating remains a dependable shield against corrosion.
By prioritizing meticulous surface preparation, employing skilled application techniques, and implementing a proactive maintenance plan, Kuwait's infrastructure and industries can leverage the full potential of protective coatings in their relentless battle against corrosion.