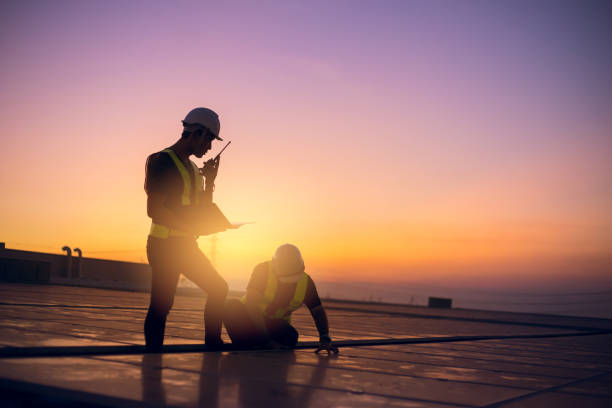
5 Types of NDT Inspection Methods in 2024
In today's world, ensuring the safety and reliability of infrastructure and equipment across various industries is paramount. This is where Non-Destructive Testing (NDT) comes into play. NDT encompasses a range of specialized techniques used to evaluate the condition of a material or component without causing any permanent damage. This allows engineers and inspectors to identify internal flaws, cracks, or defects that might compromise the integrity and performance of the material.
Ajatechsol, a leading provider of NDT inspection services in Kuwait, utilizes various NDT methods to cater to diverse needs. Let's delve into some of the most common and effective NDT methods:
1. Visual Testing (VT):
-
The most basic and cost-effective NDT method.
- Involves using the naked eye, aided by tools like magnifying glasses and borescopes, to inspect surfaces for visible defects like cracks, discoloration, or misalignment.
- Simple yet crucial in identifying surface irregularities and providing initial indications for further evaluation with other NDT methods.
2. Ultrasonic Testing (UT):
-
Employs high-frequency sound waves to penetrate the material and analyze its internal structure.
- The sound waves reflect off any discontinuities within the material, indicating potential flaws.
- Offers excellent depth penetration, making it suitable for inspecting thick components like pipes, welds, and storage tanks.
- Highly versatile and can be used on various materials, including metals, composites, and plastics.
3. Radiographic Testing (RT):
-
Utilizes ionizing radiation (X-rays or gamma rays) to create an image of the internal structure of the material on film or a digital detector.
- Similar to taking an x-ray of a human body, but for industrial materials.
- Effective in detecting internal defects like cracks, voids, and inclusions across the entire thickness of the material.
- Requires safety precautions due to the use of radiation.
4. Magnetic Particle Testing (MT):
-
Applicable only to ferromagnetic materials like steel.
- A strong magnetic field is applied to the material, and then finely divided magnetic particles (usually suspended in a liquid) are spread over the surface.
- The particles are attracted to areas of leakage in the magnetic field, which often indicates the presence of cracks or other discontinuities.
- Suitable for detecting surface and near-surface defects.
5. Dye Penetrant Testing (PT):
-
Used on non-porous materials like metals, ceramics, and some plastics.
- A colored or fluorescent dye is applied to the surface of the material, allowed to penetrate any open cracks or defects.
- The surface is then cleaned, and a developer is applied to draw the dye out of the defects, making them visible to the naked eye under appropriate lighting conditions.
- Effective for detecting surface and near-surface cracks, especially in tight corners or complex geometries.
Choosing the Right NDT Method:
The selection of the most suitable NDT method depends on various factors, including:
- The type of material being inspected.
- The size and location of the suspected defect.
- The desired level of sensitivity and accuracy.
- Cost and availability of equipment and expertise.
Benefits of NDT:
-
Prevents costly failures and downtime by identifying potential problems before they escalate.
- Enhances safety by ensuring the integrity of critical infrastructure and equipment.
- Improves product quality by identifying defects early in the manufacturing process.
- Reduces maintenance costs by facilitating targeted repairs and preventive maintenance.
By employing various NDT techniques, Ajatechsol empowers industries in Kuwait to maintain the highest standards of safety, reliability, and quality. With its commitment to advanced technology and experienced professionals, Ajatechsol ensures peace of mind for its clients by safeguarding their valuable assets.